Nodular cast iron is an important casting metal material developed in China in recent 40 years. Due to the small stress concentration caused by spheroidal graphite and the small splitting effect on the matrix, the tensile strength, plasticity, and toughness of ductile iron are higher than those of other cast irons. Compared with the steel with the corresponding structure, the plasticity is lower than that of steel, the fatigue strength is close to that of ordinary medium carbon steel, the yield ratio can reach 0.7 ~ 0.8, almost twice that of ordinary carbon steel, and the cost is lower than that of steel. Therefore, it is increasingly widely used.
Of course, nodular cast iron is not perfect. In addition to general casting defects, it will also produce some unique defects, such as shrinkage, slag inclusion, subcutaneous pores, poor spheroidization, and recession. These defects affect the performance of castings and increase the rejection rate of castings. To prevent the occurrence of these defects, it is necessary to analyze them and carry out precision casting, summarize various influencing factors, and put forward preventive measures, to effectively reduce the occurrence of defects and improve the mechanical properties and production benefits of castings.
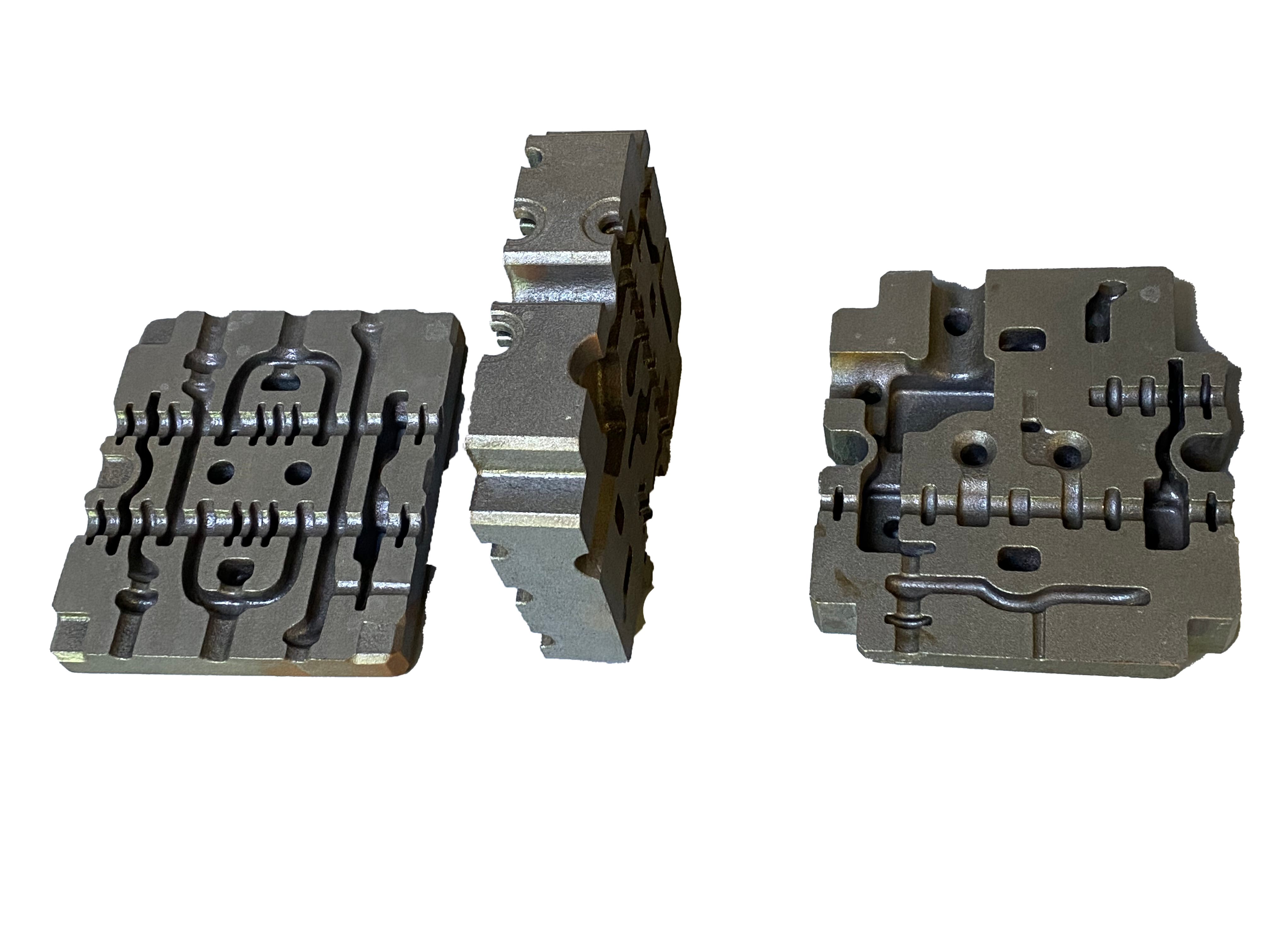
Shrinkage cavity and porosity
- influencing factors
- Carbon equivalent: increase the carbon content, increase the graphitization expansion, and reduce the shrinkage cavity and porosity. In addition, increasing carbon equivalent can also improve the fluidity of ductile iron, which is conducive to feeding. The empirical formula for producing high-quality castings is c%+1/7si%>39%. However, when the carbon equivalent is increased, other defects such as graphite floating shall not occur in the casting.
- Phosphorus: the high content of phosphorus in molten iron expands the solidification range. At the same time, the low melting point phosphorus eutectic cannot be supplied during the final solidification and weakens the shell of the casting. Therefore, there is a tendency to increase shrinkage cavities and porosity. Generally, the phosphorus content controlled by the plant is less than 0.08%.
- Rare earth and magnesium: too much residual rare-earth will deteriorate the graphite shape and reduce the spheroidization rate, so the content of rare earth should not be too high. Magnesium is an element that strongly stabilizes carbides and prevents graphitization. It can be seen that the amount of residual magnesium and residual rare-earth will increase the white mouth tendency of ductile iron and reduce the expansion of graphite. Therefore, when their content is high, they will also increase the tendency of shrinkage and porosity.
- Wall thickness: when a hard shell is formed on the surface of the casting, the higher the temperature of the internal liquid metal, the greater the liquid shrinkage, and the volume of shrinkage cavity and porosity not only increases in absolute value but also relative value. In addition, if the wall thickness changes too suddenly, the isolated thick section cannot be fed, which increases the tendency to shrink cavity and porosity.
- Temperature: high pouring temperature is conducive to feeding, but too high will increase the liquid shrinkage, which is unfavorable to the elimination of shrinkage cavity and shrinkage porosity. Therefore, the pouring temperature should be reasonably selected according to the specific conditions, generally 1300 ~ 1350 ℃.
- Compactness of sand mold: if the compactness of sand mold is too low or uneven, resulting in the expansion of mold cavity under the action of metal static pressure or expansion force after pouring, resulting in insufficient feeding of original metal, resulting in shrinkage cavity and porosity of castings.
- Pouring riser and chill: if the pouring system, riser and chill are not set properly, the sequential solidification of molten metal cannot be guaranteed; In addition, the number and size of risers and the connection with castings will affect the feeding effect of risers.
- preventive measures
- Control the composition of molten iron: keep high carbon equivalent (>39%); Try to reduce the phosphorus content (<0.08%); Reduce the residual magnesium content (<0.07%); The residual amount of rare earth oxide is controlled between 0.02% and 0.04% by using rare earth magnesium alloy.
- The process design shall ensure that the casting can continuously supplement high-temperature molten metal from the riser during solidification. The size and quantity of risers shall be appropriate to strive to achieve sequential solidification.
- If necessary, cold iron and subsidies shall be used to change the temperature distribution of castings, so as to facilitate sequential solidification.
- The pouring temperature shall be 1300 ~ 1350 ℃, and the pouring time of a package of molten iron shall not exceed 25min to avoid spheroidization recession.
- Improve the compactness of sand mold, generally not less than 90; The sand shall be bumped evenly, and the water content shall not be too high to ensure that the mold has sufficient rigidity.
Searching for a the rock cast iron, cast iron and steel, heuck cast iron supplier, wholesaler, manufacturer from China, you can get high-quality products at a nice price.